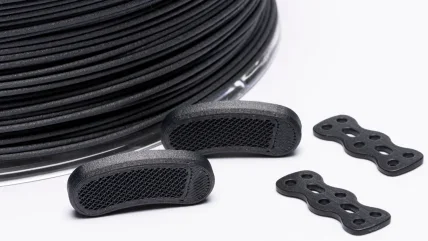
For bone plates and other reconstructive implants, additional properties such as adaptable rigidity and flexibility are paramount.
To gather more insight on the possibilities of this latest smart biomaterial, Medical Device Developments reaches out to Dr. Philip Engel, head of the Medical Systems for Europe segment at Evonik High Performance Polymers.
Evonik is the developer of an innovative 3D printable carbon-fiber reinforced PEEK filament and is one of the key pioneers in polymers for 3D printing. For more than 20 years, Evonik’s smart biomaterials having been enabling medical device manufacturers with seemingly limitless potential in producing patient-specific medical applications with its polyether ether ketone (PEEK) products, known as VESTAKEEP®.
What can you tell us about the latest product from Evonik for medical device development?
Evonik’s latest development is the carbon-fiber reinforced PEEK filament for medical 3D-printed long-term implants. The filament comes in two versions: VESTAKEEP® iC4612 3DF with 12% carbon fiber, and VESTAKEEP® iC4620 3DF with 20% carbon fiber content. These two grades give medical device developers options depending on the required strength and bending properties of 3D-printed implants like bone plates and other reconstructive prostheses.
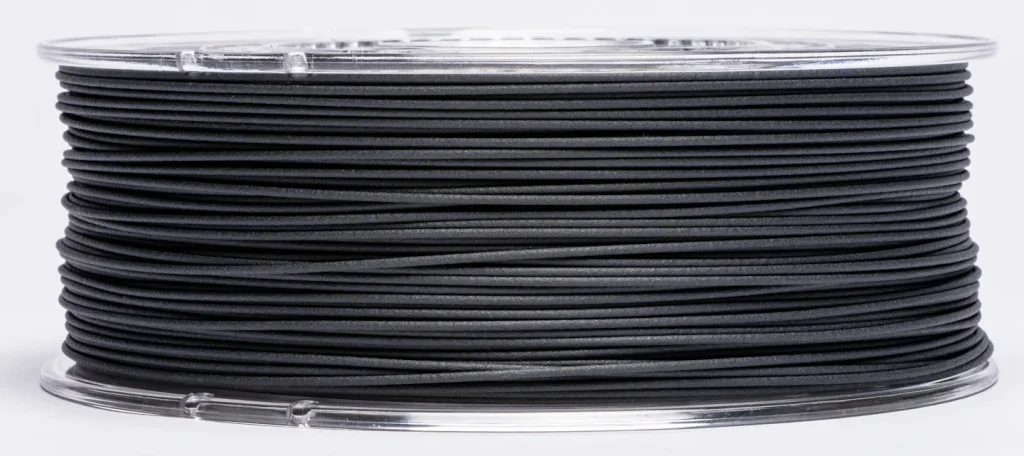
The filament itself features a 1.75mm diameter, and is processable with conventional PEEK printers using fused filament fabrication (FFF).
What are the advantages of 12% and 20% carbon fiber content?
In medical implant technology, metals like titanium are still often used, but these can be sometimes too rigid and lead to high stress on the bones. The material also causes strong X-ray artifacts. In such cases, carbon-fiber reinforced PEEK presents a great alternative as it offers greater rigidity and more physiological mechanical properties.
The choice between 12% and 20% carbon fiber content, as well as use of 3D printing technology, give customers unprecedented flexibility and a wide range of applications.
What are some of the key benefits of these filaments, compared to traditional products?
By finding a way to incorporate carbon fiber into the PEEK material, the overall stiffness is increased by a factor of 3 or 4, which makes the filament suitable for medical applications requiring a high level of stiffness. Suitable applications include bone plates, where traditional PEEK without carbon fiber would be too elastic.
Another benefit of these filaments comes from our technological ability to tailor the properties of the material to the printing process used. This is important because fiber-reinforced materials behave anisotropically, meaning their mechanical properties depend heavily on the orientation of the fibers.
With our technology, we are able to orient the carbon fibers in a certain direction for extra strength, which leads to very high mechanical properties in the printed end-product.
This adds more benefits than fiber-reinforced parts produced by injection molding, which by nature of the process, has limited possibilities for controlling the end-product’s mechanical properties.
Where can we learn more about this and other PEEK solutions for medical device development?
At Evonik, we are always focused on developing materials based on the needs of customers, and offer a wide range of customized biomaterials for medical equipment and device applications. From November 11 to 14, our experts will be on hand to present our carbon-fiber reinforced PEEK filament at the COMPAMED trade show, in Düsseldorf, Germany.
Additionally, more details on our ready-to-use, implant-grade VESTAKEEP® PEEK filaments are available on our website.