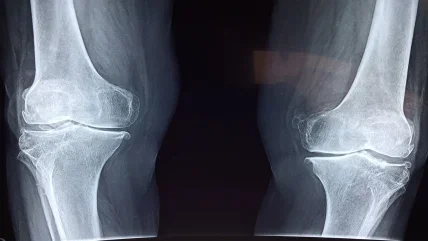
Ceramic materials are inorganic and non-metallic – essentially everything that is not a polymer or a metal. They can be divided into four main categories: traditional ceramics, refractories, cementitious materials and advanced ceramics. The word ceramic is derived from the Greek word ‘keramos’, meaning ‘potter’ or ‘pottery’, but the use of the material spans much wider than the name might suggest.
Traditional ceramics are based on clays, which provide everything from bricks to cups and tiles to washbasins. Refractories can tolerate high temperatures and chemical attacks, and are often used to line furnaces for melting metals and glass, or for firing other ceramics. Cementitious materials are based on cements and mortars, and are used heavily in the construction industry.
Advanced ceramics, which have a variety of engineering properties, can be categorised into three main types. This includes electroceramics, which are used throughout the electronics industry, for items such as communications equipment and display technology. Engineering ceramics are used for manufacturing all different kinds of materials, including those used in energy generation and storage and defence.
Bioceramics are ceramics used in healthcare, in everything from artificial bones and joints to dental materials. These can be further divided into two categories: bioinert and bioactive. The former requires a layer of tissue to separate the bone from the ceramic, whereas the latter can facilitate a direct connection between the body and implant to promote healing.
The Ceramics Society has estimated the total global annual ceramic market to rise to approximately $287 billion by 2022. Advanced ceramics are expected to be the fastest-growing segment, reflected in the prediction that the global annual medical ceramics market will reach $26 billion by 2025.
Rise above the pack
The popularity of ceramics in medical devices, and other industries, is due to their ability to deliver performance that other materials simply cannot. Ceramics are particularly robust, and can survive extreme stresses, temperatures, nuclear radiation or highly aggressive chemicals.
“The main applications of ceramics in healthcare include use in hip and knee replacements as well as dental restorations,” says Roger Narayan, professor at the Joint Department of Biomedical Engineering at the University of North Carolina and North Carolina State University.
Hip replacements are now a routine and effective successful orthopaedic implant, and currently more than 50% are made from a ceramic ball, and some from ceramic cup. Ceramics offer a number of advantages that make them particularly suitable for implants, as discussed by Andy Weymann, chief medical officer at Smith & Nephew, in a previous interview with Medical Device Developments.
“Firstly, ceramics are harder than metals,” says Weymann. “They have better corrosion resistance and can withstand body fluids. They also provide low-wear bearing couples when combined with polyethylene or when used as ceramic on ceramic. This all helps to reduce the risk of the implants loosening and the risk of revision.”
Biocompatibility is a key issue in implants, and one of the key advantages of ceramics, as highlighted by Eileen de Guire of the American Ceramic Society. “The body’s interior is a very chemically active place, which can lead to corrosion or dissolution of metals,” says de Guire. “Ceramics also provide structure and highly tuneable compositions.”
All of these properties remain a work in progress. “The evolution towards more biocompatibility and better device design is continual,” says de Guire. “Hip implants, for example, have evolved to accommodate anatomical differences between men and women; ball and socket materials are more wear-resistant; bone cements adhere better and longer.”
Among the variety of ceramics available, certain materials are more suitable than others for this application. “Alumina, zirconia and silicon nitride are nearly inert ceramics that provide wear-resistant and corrosion-resistant performance to medical and dental implants,” explains Narayan. “Hydroxyapatite and Bioglass (R) are bioactive ceramics that form direct bonds with bone; these materials are also used to replace bone and dental tissues.”
Limitations of ceramics
Despite the advantages offered by ceramics, they have several downsides. “Ceramics are generally brittle,” says Narayan. “Since the strength of ceramics is highly dependent on the presence of flaws, flaw-free ceramics are desirable. Nearly inert ceramic coatings can be deposited on the surface of metallic medical devices to impart high hardness, wear resistance and corrosion resistance.”
Due to these limitations, these materials are not always sufficient by themselves. Depending on the application, a range of high-tech materials can be used in conjunction with them. For example, the combination of a titanium hip prosthesis with a ceramic head and polyethylene acetabular cup. These can reduce friction and offer an increased resistance to abrasion when compared with ceramics alone, while simultaneously retaining the toughness of metal. “Ceramics provide limited options in terms of design flexibility, for example,” says Weymann. “They are also known to be less hard than other materials, so they may not be suitable for all patients. They need to be used for the right applications and used with care.”
The ceramics sector is evolving, with a variety of uses currently being explored. “In the beginning, materials like ceramics were used for replacement parts: hips, knees, teeth, and fasteners to hold broken bones together,” says de Guire. “These are still very important applications, especially for the people who are suffering or injured.”
$287 Billion
The estimated total global annual ceramic market by 2022.
The Ceramics Society
There are a range of novel applications for ceramics, far beyond implants. “Ceramics, like lead zirconate titanate, exhibit the piezoelectric effect (the ability to generate an electric charge in response to applied mechanical stress) are being used in sensors, including microcantileverbased antibody sensors and actuators, such as ultrasonic transducers.”
This hasn’t consistently changed initial perceptions though. “Most people think of implants when they hear the term ‘medical devices’– things like hip implants and fasteners,” says de Guire. “But the field encompasses much more, as it relates to ceramic and glass technology.”
For example, glass spheres are able to deliver radiation or chemotherapy payloads directly to cancers. Glass fibres facilitate repair from open wounds. Ceramic nanofibres are being used for breathalysers capable of detecting disease biomarkers, and tattoo-like sensors are being developed for diabetes monitoring.
These applications arise from observations about the way in which ceramics, and related materials, interacted with the body, and learned more about the underlying mechanisms. This has led to developments such as bone scaffolds made of HAp. The scaffold provides mechanical structure and chemical building blocks as the bone grows into it and subsequently absorbs the scaffold.
Some of the most exciting research is investigating ways that ceramics can contribute to building new body parts. “For example, would it be possible to 3D print a new kidney and eliminate the tethering of dialysis?” says de Guire. “What about other body parts that hugely impact quality of life, such as urethras or tracheas?”
The path ahead
It’s clear that ceramics is an area worth watching over the next few years, with a number of promising developments on the horizon. “New ceramics that will reach the market in the next few years will include more resilient hip and knee replacements, higher-quality dental restorations, new materials for wearable devices and drug delivery, as well as new materials for healing of bone,” says Narayan.
There are also some interesting developments within diagnostics that take advantage of the unique atomic structure and defect chemistry of ceramics. This includes research by Pelagia-Irene Gouma, the Edward Orton Jr, chair in ceramic engineering at the Ohio State University, who has been working on breathalysers that can detect organic markers for serious diseases. The device uses nanofibres of transition metal oxides, such as tungsten oxide. The nanofibres provide a large surface area and the defect structure of the oxide creates voids, in which organic compounds fit. The oxide compositions can be tuned to specific compounds that mark diseases.
In light of the highly regulated nature of the medical device industry, it’s important to be realistic about the time frames of progress. Regulators, such as the FDA, need to keep up with R&D, and ensure medical devices based on emerging and evolving technologies such as ceramics can be brought to market as efficiently as possible.
These hurdles aside, as ceramics continue to evolve in terms of biocompatibility, strength and longevity, they will be able to be used in a wide range of exciting medical applications. The material may have its roots in the ancient world, but its potential will extend long into the 21st century and beyond.
The history of the piezoelectric effect
The direct piezoelectric effect was first seen in 1880, and was initiated by the brothers Pierre and Jacques Curie. By combining their knowledge of pyroelectricity with their understanding of crystal structures and behaviour, the Curie brothers demonstrated the first piezoelectric effect by using crystals of tourmaline, quartz, topaz, cane sugar and Rochelle salt.
Their initial demonstration showed that quartz and Rochelle salt exhibited the most piezoelectricity ability at the time. Over the next few decades, piezoelectricity remained in the laboratory, something to be experimented on as more work was undertaken to explore the great potential of the piezoelectric effect. The breakout of the First World War marked the introduction of the first practical application for piezoelectric devices, which was the sonar device.
This initial use of piezoelectricity in sonar created intense international developmental interest in piezoelectric devices. Over the next few decades, new piezoelectric materials and new applications for those materials were explored and developed.
During the Second World War, research groups in the US, Russia and Japan discovered a new class of human-made materials, called ferroelectrics, which exhibited piezoelectric constants many times higher than natural piezoelectric materials.
Although quartz crystals were the first commercially exploited piezoelectric material and are still used in sonar-detection applications, scientists kept searching for higherperformance materials. This intense research resulted in the development of barium titanate and lead zirconate titanate, two materials that had very specific properties suitable for particular applications.
Source: Nanomotion